
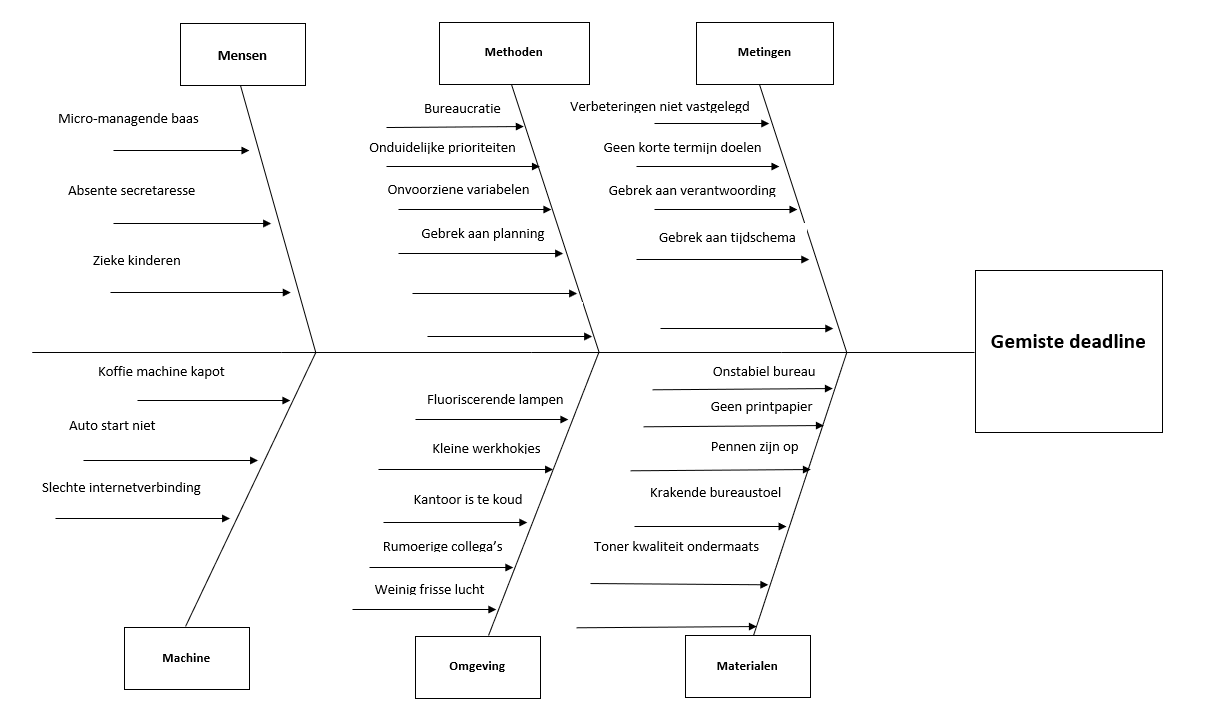
The cause-and-effect diagram plays a central role in Six Sigma quality programs.

Six Sigma, and the Cause-and-Effect Diagram Once these steps have been completed, transfer the major categories of causes and the sub-causes to the chart as major arrows ("fishbones") and subheaders (of course, the Cause and Effect procedure of STATISTICA

These resources (or "variables") that affect the final quality of the software could, for example, be classified into the generic categories (e.g., see Seder, 1962) of For example, producing bug-free computer software of superior quality requires a very complex process that involves numerous different types of resources. While the example discussed above is rather trivial, when troubleshooting complex production or service processes, creating this diagram can be immensely helpful. You can also further "augment" this chart (using the custom drawing and other tools of STATISTICA graphics) by adding various sub-sub causes, causes that you ruled out, solutions you have tried, etc.Ĭategories of Causes, Tools for Creating the Diagram You could now use this map as a guide to troubleshooting the problem you encountered turning on your reading light.
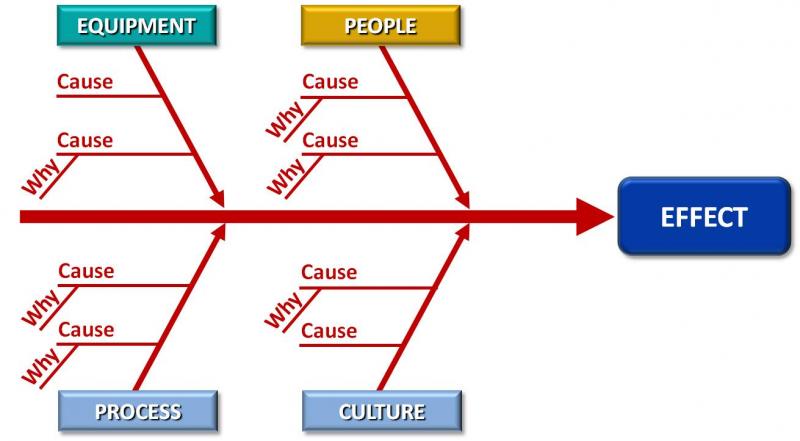
Lamp), and 2) the individual factors or causes that can be classified into these major categories (e.g., Usually, the chart is constructed by identifying 1) the major categories of causes that affect the process (in this example It includes the raw information coming in, on through the final output that is delivered to the customer.The cause-and-effect diagram shown above (adapted from Rath & Strong's Six Sigma pocket guide, 2000) spells out the various potential causes of the problem encountered. Product: This final “P” refers to the information/service product that is being processed.It may include corporate wide systems, or individual software packages installed on a computer. Program: Program, in this usage, refers to software programs.Plant: The physical layout of the building and the proximity to other locations fall into this category.Be careful not to assign process, policy, or program causes to people. People: The makeup, size, and skills of a team all have an impact on the effect you are looking at in your fishbone diagram.Informal processes are sometimes called the “hidden factory”, or the “hidden office.” Process: Processes may be formal or informal.The degree of flexibility in responses to customers, for example, is often guided by policy-driven rules. Policy: Policy affects office environments much more than they affect the shop floor.
